国内外学者针对环模制粒成型技术进行了大量研究,取得了一批研究成果,为高效节能制粒技术的研究提供了一定的研究基础。本节从成型机理、制粒生产率、制粒能耗、颗粒质量、制粒稳定性及核心部件寿命等几个方面对国内外的研究现状进行综述。
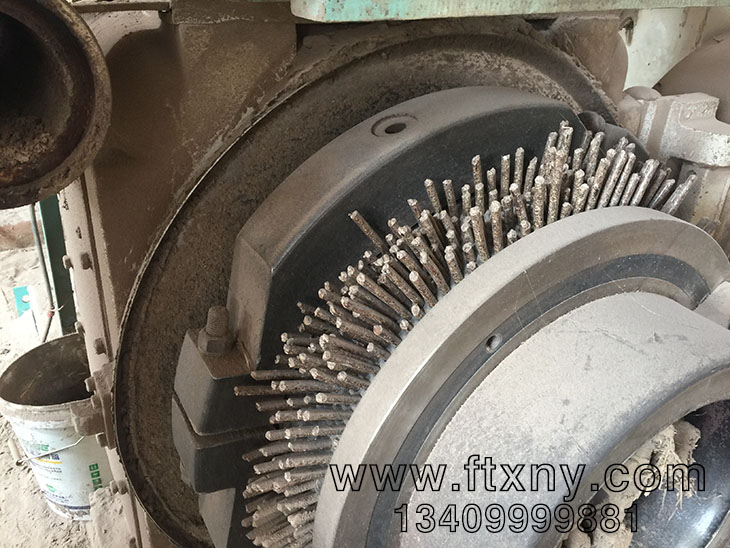
挤压机理的研究主要集中在三个方面:环模制粒挤压成型力学模型的研究;环模制粒挤压成型压缩过程的研究;环模制粒挤压成型过程粉体颗粒间内部结合机制的研究。
针对环模制粒挤压成型力学模型,在国外,丹麦技术大学开展的“制粒过程基础性研究”项目(EFP-2005 Project(33031-037》对于木质粉体制粒进行了一系列基础性研究,项目组成员Holm等建立了木质粉体在环模孔内挤压的力学模型,推导出了挤压力的方程式,并分别用小型试验制粒机和单孔制粒单元试验装置进行了试验验证;为了解决力学模型关系式中三个变量(泊松比、摩擦系数和预加作用力)相互耦合而难以确定的难题,又对力学模型方程进行了改进。在国内,曹康对制粒的机理、工艺进行了全面的论述,对挤压区的受力状况进行了比较详细的力学分析;张维果、吴劲锋通过对不同粒度的苜蓿草粉进行压缩实验,得到了颗粒挤出力与粉体粒度、密度之间的关系,并建立了数学模型;周晓杰、王春光采用电测技术,选择初始密度和压缩速度为试验因素,对苜蓿草径向力进行测试研究,获得了压缩密度、初始密度和压缩速度对苜蓿草径向压缩力的影响规律;武凯针对粉体环模制粒成型理论进行了一系列研究,建立了环模制粒挤压过程完整的力学模型及扭矩模型。
针对粉体物料的压缩过程,杨明韶等开展了秸秆类物料开式压缩实验,对其流变学特性进行了研究;白炜等进行了三种秸秆颗粒冷态压缩成型的开式实验研究,将其压缩成型特性曲线定义为松散、过渡、压紧和推移四个价段,并对前三个阶段进行了回归分析;孙启新等将生物质成型过程划分为松散、压紧和固化三个阶段),认为固化过程是塑性变形和黏性变形的结合;对于成型过程中物料的变化规律,Rehkuglar等利用流变力学模型进行了分析;董玉平、回云埔则应用有限元软件模拟了成型过程的应力应变和温度场,证明存在适宜的温度使原料流动性增强,成型更加容易。
针对粉体颗粒间内部结合机制,Lindley将成型物内部的黏结力类型和黏结方式分成五类:固体颗粒桥接或架桥、非自由移动黏结剂作用的黏结力、自由移动液体的表面张力和毛细压力、粒子间的分子吸引力或静电引力、固体粒子间的充填或嵌合,认为生物质燃料特性可以用上述的一种或几种黏结类型来解释其内部的成型机制;田潇瑜研究表明,秸秆燃料的内部结合形式主要为机械镶嵌和天然黏结剂黏结;Kaliyan利用电子扫描显微镜(SEM)观察了不同方式制出的玉米秸秆颗粒和柳枝稷颗粒,发现颗粒之间的结合方式主要是固体桥接,并且通过紫外荧光照片发现固体桥接主要是由天然黏合剂(纤维素、蛋白质)形成,因此提出了有必要调节物料的水分含量和制粒温度来使得这些黏合剂融化,进而形成质量更好的颗粒;霍丽丽研究表明,玉米秸秆等生物质燃料(环模成型)的微观成型机理为分层间断性压缩,分为中心层、过渡层和表层,层与层间距为25~40Um;吴云玉则研究了生物质颗粒微观成型机理,建立了微观接触几何模型,认为压辊对原料的正压力F与生物质颗粒表面斜角al的余弦成正比。
2、制粒成型生产率
针对提高制粒成型生产率的研究主要集中在两个方面,一方面是针对现有结构提出参数选择、优化规范,另一方面是通过新的结构提升制粒效率。
针对制粒机结构参数对制粒生产率的影响,陈炳伟指出,环模和压辊的结构参数对环模制粒机的生产效率影响很大,选用大直径环模和压辊可以提高制粒生产率,但压辊数目与模辊直径比有相互制约的关系,因此单纯增加压辊个数并不一定能提高环模制粒机的生产效率。王敏、李艳聪研究了环模转速与制粒生产率之间的关系:王敏研究表明,环模制粒机的生产率与环模的转速没有严格的正反比关系,环模存在最佳转速范围对应最高的生产率;而李艳聪则通过实验研究了环模线速度和饲料加工产量之间的关系,得出制粒机产量与环模线速度之间存在拐点,即对应特定的物料,制粒机采用合理的线速度可使得制粒产量最大。环模表面开孔率方面,高放研究表明,环模开孔率直接影响到制粒机的生产效率,理论上,环模表面的开孔率越大,制粒机的生产率越高,但是开孔率的大小也直接影响到加工的难易程度及环模的强度,因此在保证环模有足够的强度及加工容易的情况下,应尽可能地提高环模开孔率。辊模间隙也影响到环模制粒机的生产效率,林云鉴研究表明,辊模间隙过大时,物料打滑,生产率降低;而当间隙过小时,粉料经挤压温升加剧,水分蒸发较快,使物料干结堵塞模孔,生产率也降低。此外,Blank对制粒过程进行了优化分析,研究了如何在保证加工质量的前提下提高加工效率;Wuc28]建立了环模制粒生产率模型,对影响生产率的各因素进行了分析。
除了针对现有结构参数对制粒机生产率的研究外,专利文献中提出了多种新型结构以提高制粒效率。方亨志提出了一种带切线搅拌桨的混合制粒机,在搅拌机构中设置了搅拌桨和传动装置,并将搅拌桨按其圆周的切线方向均匀分布放置,可以提高物料的混合效果,并提高生产率;迈斯特提出在制粒机中使用切割转子,该转子的外周面上布有切割的刀片都由一驱动系统带动旋转,在制粒过程中对颗粒可以进行及时地定向切割,有助于效率的提高;某公司提出了两种高效率制粒机:环模和压辊可同时转动的制粒机)和双环模内置式制粒机,环模、压辊同时转动可减小堵机概率,进而提升效率,而双环模内置式制粒机增置了内环模,在内环模壁上同样设有若干径向的模孔,这样两个环模都可以进行制粒,工作效率得到提高;某厂提出在生物质颗粒制粒机中使用过盈连接的双层环模来增强环模疲劳强度,可压制木质颗粒以及在重载荷下连续运转,进而可提升生产效率;某公司所提出的双环模式制粒机是将两只环模安装在主被动轴上,两者之间形成压力角相向转动,生产效率可成倍提高;张惠明提出了一种压辊式碾压制粒机:在机架上设置了左右滑动的滑模,可以根据需要调节颗粒的密度和长短,具有较高的生产率;尼罗有限公司提出在压实制粒机中设置水平放置的旋转滚筒,其中心轴偏心,工作时多个压实装置传递力量给颗粒以取得高的压实效果,可进行连续压实,效率较高。
3、制粒成型能耗
如何降低制粒能耗是国内外研究的热点,制粒能耗的降低不应以降低颗粒质量为代价,因此研究环模制粒能耗实际上也就是研究在保证颗粒质量的前提下如何降低单位产量能耗,即在提高颗粒质量和降低能耗之间寻求一种平衡。
由于影响环模制粒机能耗、产量及颗粒质量的因素很多(如物料含水量、颗粒大小及分布、添加剂、环模尺寸、模孔尺寸、压辊尺寸、环模转速、进料速度、制粒间隙等),且这些参数间大多存在耦合关系,进行制粒系统整体优化非常困难。国内外开展的相关研究主要集中于工艺参数及物料理化参数的优化,且大多只是对其中一两个因素进行理论分析和实验研究。
林云鉴等分别利用实验室制粒系统和饲料厂制粒系统,考察了制粒工艺参数(水分、长径比、模辊间隙)的改变对生产率、电耗、饲料颗粒质量的影响,为含谷物高的配合饲料的制粒工艺参数的选择提供了参考依据;王敏分析了模辊间隙大小对制粒性能(生产率、电耗和颗粒加工质量)的影响,结果表明,在一定范围内增大环模、压辊的间隙,会增大黏料层厚度,进而使得生产率下降、吨电耗上升,但加工质量会有所提高;Rolfe研究表明,环模转速的提高使物料高度减小,进而挤压物料的力减小,但是颗粒的温度提高了,制粒过程消耗的机械能增加,综合这些结果,制粒的能耗表现为增大;武凯根据建立的能耗模型分析了环模速度对制粒能耗的影响,结果表明,随着模速的提升,制粒能耗逐渐攀升;Tabil等建立了能耗与颗粒耐久性间的关系模型;Nielsen等对不同材质的木屑颗粒进行了实验对比分析,分析了提取物的含量对制粒机的能耗的影响,结果表明,树脂、脂肪族化合物、固醇等可以减小物料被挤压入模孔中的力,降低制粒机的能耗,但木屑的保压时间对挤压力及制粒机的能耗影响不明显;Mehrdad等对木屑水分含量、木质材料新鲜程度等不同参数下的物料作了制粒过程的对比试验,发现在工艺过程中优化这些参数可以提高颗粒品质和降低能耗;Nielsenc对不同制粒特性的木屑进行了分析研究,发现加工横向纤维方向的生物质物料时产量高、能耗低。
在工艺技术与结构技术改进方面,某公司提出了一种饲料制粒专用润滑液及其制备方法,将一种具有润滑、黏合和诱食三种功能的专用润滑液加人物料中,制造颗粒可以显著地降低能耗;施迎春提出了一种生物质颗粒燃料制取工艺,使用该工艺的制粒机采用相向旋转并外切的双环模,环模上布有若干压制通孔,孔心均指向圆心,该结构可使单位能耗大幅减少;某公司发明了一种环模和压辊间隙调整装置:由于压辊装置安装在偏心轴上,转动活动花板可自由调整模辊间隙,调节方便、制粒稳定,有助于降低能耗;郑忠义提出在异形组合式环模中将成型孔的出料口做成圆形或矩形扩孔出料口,并使用了环式腰带连接件,挤压制粒时模孔不易堵塞,可降低能耗的浪费;尹小林提出,在节能型环模滚轮挤压成型机中采用齿轮控制环模和滚轮之间的滚动,不需要经常性地调整间隙,可减少堵塞现象,提升制粒稳定性,进而可以降低能耗;某公司提出在压辊壳的圆周方向开设弧形凹槽,弧形槽沿壳体轴向由两端向中间延伸呈弧状,可解决现有技术中壳体易磨损、卷料性差的难题,保证壳体磨损均匀而且不易堵塞,有助于达到节能的目标;陈康海提出,采用新型刀片紧靠在环模孔出料口,致使切割的颗粒端面整齐、使用物料减少,返回料也会随着减少,进而可有效降低能耗。
4、成型颗粒质量
制粒成型质量直接影响颗粒的存放、运输、热值等指标,国内外有关制粒成型质量的研究主要集中在结构参数与工艺参数对颗粒质量的影响方面。
Kaliyan等指出,原料特性、预处理过程和成型设备都会影响成型产品的强度和耐久性;并就物料理化性质、水分含量、添加剂、制粒机参数及制粒工艺参数对颗粒质量的影响进行了综述,为制粒参数的选择提供了参考。
Obidzinskir54]应用实验型制粒机研究了制粒机结构参数(环模孑L径长度、模辊间隙)对饲料颗粒质量的影响,结果表明,随着孔径长度和模辊间隙的增加,颗粒密度和动态耐久性也随之增加,且颗粒质量与动态耐久性之间存在线性关系;Colovicc55]对三种具有不同长径比的制粒机制粒过程进行研究,结果表明,随着长径比的增大,颗粒硬度、能耗和颗粒耐久性都会随之增大,且增加水分含量可以有效地降低能耗,但同时也可能使得颗粒耐久性下降;Hernandez等应用单元制粒装置研究了羊饲料制粒的最佳参数(含水量、温度及长度),并进行了实际生产验证,结果表明,此种选择优化参数的方法简便易行;Tumuluru利用单孔制粒单元和实验性制粒机对影响小麦基底型酒糟颗粒质量的相关因素(水分含量、温度和环模孔尺寸)进行了实验研究,建立了回归模型并进行了数据分析,并且提出了相关优化参数。
Caronec58]研究了制粒工艺参数(压力和温度)和物料性质(水分含量和颗粒大小)对橄榄树枝条颗粒的质量(密度和耐久性)的影响,结果表明,温度影响最大,其次是水分含量和颗粒大小,影响最小的是挤压力;Relova就加勒比松制粒过程中颗粒尺寸、水分含量和挤压压力对颗粒质量的影响进行了研究,结果表明,挤压力影响最大、水分含量次之、颗粒尺寸最小,且当挤压力增大到一定程度后继续增加对颗粒质量影响不大;黄晓鹏等试验得到,对苜蓿制粒密度影响的强弱依次为挤出力、含水率、草粉粒度;Mani等研究得出,成型压力、颗粒尺寸和含水率对小麦和玉米秸秆的成型密度均有影响;陈晓青研究表明,含水率和进料速度还对玉米秸秆成型燃料裂纹的形成有较大影响;廖娜指出,玉米秸秆等生物质燃料的松弛特性与原料的木质素含量相关。
其他相关的研究结论包括:压力是决定生物质燃料品质的主要参数;增加成型压力和保压时间以及加入添加剂会提高燃料品质;成型温度越高,燃料的抗跌碎和抗渗水能力越差;等等。
5.制粒稳定性与核心部件寿命
环模制粒稳定性,既指制粒过程稳定、颗粒质量有保证,又指制粒机运行稳定,关键部件可靠性高。从制粒机实际运行情况来看,我国制粒机相对于国外同类产品而言依然存在关键部件使用寿命低,振动、噪声大等问题。作为环模制粒机关键部件,环模、压辊工作时长期承受压力和物料摩擦,工作条件恶劣,容易失效,是目前环模制粒成型设备存在的主要问题。环模与压辊的失效形式以结构破坏和过度磨损为主,与材料、结构、热处理方式及物料特性、生产条件密切相关。目前,对于环模、压辊寿命的研究主要集中在结构受力分析、摩擦磨损机理分析、模具材料、模具结构、热处理工艺等方面。
张炜等对三种不同倒角的环模结构型孔进行了有限元静力分析,认为60°倒角孔的变形小,结构最好;申树云等通过受力分析得出生物质成型机模孔的最佳长径比为5:1;刘超等研究了生物质模具锥角与应力的关系,认为最佳锥角取值为5. 5°~6. 0°;邓勇等对制粒机环模进行了均匀载荷和非均匀载荷的有限元分析,得出了非均匀载荷是导致环模两端磨损严重的重要原因;施水娟等建立了环模挤压力学模型,并进行了数值模拟分析,研究表明,环模与压辊的两侧变形大,中间变形小,环模与压辊受到了不均匀载荷的作用;武凯等对制粒过程中模孔挤压过程进行了仿真分析,得出结论:相比于锥面孔口,使用曲面孔口可以减少磨损。
张炜、吴劲锋对苜蓿草粉制粒机环模失效行为进行了研究,认为环模磨损失效与疲劳失效存在一定关系,随着磨损的加剧,环模的模孔内壁壁厚发生变化,降低了环模的抗疲劳能力,环模表面在疲劳剥落和显微切削两种磨损机制作用下产生表面的材料流失,最终导致环模的磨损失效;吴劲锋建立了环模结构优化设计的数理模型,并利用苜蓿草粉进行试验得到影响磨损各因素的强弱顺序依次为转速、物料颗粒尺寸和载荷,指出环模磨损主要是由塑性变形和显微切削两种磨损机制造成的,植物纤维与金属间相互作用的摩擦力是造成该类磨损的主要原因,生物质成型模具以磨料磨损为主,苜蓿等生物质原料对金属表面的磨损为硬、软磨粒共同作用的结果;孔雪辉对生物质环模的磨损问题进行了研究,建立了模孔的等磨损优化数学模型;霍丽丽指出,压辊磨损除了由于原料中含有硅酸盐成分、杂质、水分等易加速腐蚀、磨损的物质外,物料的不均匀分布也是十分重要的影响因素,研究表明,进料侧压辊面比其他位置表面多磨损约40%。
针对环模的磨损问题,朱滨峰等研究了一种新型预应力环模,使环模的淬硬部分受到一种预应力,以抵消环模工作时压辊对它施加的部分或全部应力,进而降低环模工作时的总应力,提高环模的使用寿命;杨毅指出,为提高模具寿命,应确保材料的Cr含量在12. 5%以上;孙晶锋等对45钢、9SiCr和60SiMn试样进行磨料(紫花苜蓿)磨损试验,结果表明,9SiCr韧性和磨损性能最好;陈志光等通过试验表明,4Cr13环模经低温碳氮共渗、真空高压气淬后,其使用寿命显著提高,并指出增加模具硬度可提高其耐磨性能,但太硬容易发生脆性断裂,设计时应同时考虑材料的硬度和韧性。此外,罗锐指出,环模孔的堵塞要及时清理,否则不仅影响制粒机的生产率、颗粒质量,还会影响制粒机的使用寿命;姚修伟指出,提高环模的开孔率可以很大程度上提高制粒机的生产率,但是孔的数量多,势必使孔之间的间距减小,环模的强度和耐磨性不但差,而且易断裂,环模的使用寿命大大缩短。
制粒过程稳定性方面的研究主要集中在如何实现物料均布、如何实现制粒机的防滑防堵等方面。目前研究成果主要是在制粒机结构方面进行设计和改进,并以专利的形式展示出来。在实现物料均布方面,有强制喂料装置、匀料装置和旋转进料装置;在防滑防堵方面,提出对压辊表面形状进行改进,设计了防滑压辊壳以提高物料攫取能力,避免物料在压缩情况下向两侧滑动;并通过增加限高板的方式来限制物料高度进而避免制粒机堵机。
综上,环模制粒成型技术是一种先进的颗粒成型工艺技术,集成了机械工程、粉体力学等多学科知识,在生物质固化成型、饲料加工等国民经济重要技术领域应用广泛。当前,环模制粒成型技术基础理论体系的不完备严重制约了我国相关产业的发展,研究环模制粒机理、技术与装备对发展清洁能源、促进三农发展、降低环境污染具有非常重要的理论意义与实用价值。
转载请注明:河南省富通新能源生物质颗粒机www.ftxny.com